Prefabrication And Modularity In Bim Construction
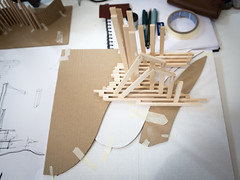
- Here’s An Opinion On:
- House And Land Packages Mudgee
Prefabrication and Modularity in BIM Construction
by
Joel Darras
As Building Information Modeling continues its march through the AEC industry, its effects and advantages for construction management are coming more into the spotlight. BIM construction is a fundamentally different animal than past practices. In terms of the relationship between the owner, designer and builder, in how construction is actually accomplished, and in terms of the bottom-line, BIM construction is changing in subtle and radical ways how a project is executed. Construction managers are now included in the design process, prefabrication is increasingly used and build times, change orders and site logistics are all positively affected by BIM construction.
The construction industry has lagged far behind most other industries in leveraging modern technology for productivity gains.One of the most glaring facts about the construction industry as a whole is encapsulated by the US Department of Commerce, Bureau of Labor Statistics finding that the construction industry has had continual losses in productivity since 1964, in stark contrast to all other non-farm labor, which has almost doubled productivity in the same 40 years.
One of the prime reasons for declining labor productivity in the construction industry has to do with the traditional process by which a project is conceived and delivered. The design-bid-build paradigm is a fragmented process, where the owner contracts with separate professionals for the design and construction of the project, and each phase follows the previous one. Any collaborative involvement between the design professionals and the construction professionals is highly limited, leading to change orders, errors and other issues when the best-made plans are confronted with construction site reality.
BIM construction provides the necessary platform and processes for reversing this trend. The National Research Council of the National Academies identified BIM construction enabled prefabrication and modularity as important components to improve the efficiency and competitiveness of the US construction industry in a 2009 report. As 3D modeling and parametric design make constructability part and parcel of the design process, construction managers are increasingly brought in early in the project s design phase, to evaluate the practicality of a design. This involvement has driven what some call the oldest new idea in construction. Prefabrication, and modularity, bring to bear in the construction industry practices that Henry Ford discovered well over a hundred years ago. Fundamental to this is the decoupling of manufacture from assembly. Instead of costly, time-consuming onsite fabrication and fitting of parts, prefabrication in a controlled environment allows for a reduction in labor, faster completion times, less waste and change orders. This is particularly true in the finish and detail portions of a building, as well as the skin and fa ade systems.Modular components are then brought to the site for efficient assembly. This is neither new nor particularly foreign to the construction industry.
One of the earliest examples of modern prefabricated construction was the magnificent Crystal Palace in London, built for the Great Exhibition of 1851. Made of cast-iron and glass, the Palace was longer than Versailles and higher than Westminster Abbey. The building was completed in less than 200 days, from conception to occupation. 3300 iron columns, 2150 iron girders, 250 miles of sash bar, 293,635 panes of glass. The crucial detail is that these all conform to a basic 24 foot module, allowing the manufacture to be contracted to several foundries and glass factories. The entire structure was dismantled in 1852 and moved to another site, reassembled and stood until fire destroyed it in 1936.
The Hilton Palacio del Rio in San Antonio was designed, built and occupied for the Texas World Expo in 202 working days! A 500 room deluxe hotel, still in use today, had each room factory built and placed by crane in 46 days.
Most recently, in Lin Gang Industrial Zone in Xiangyin County, a 17,000 square meter hotel known as T30 was completed in an astonishing 15 days! Over 350 rooms with restaurant, gym, swimming pool and underground parking, 93% of the building was pieced together onsite with premade assemblies. Earthquake resistant up to magnitude 9, the building boasts quadruple-paned windows, external solar shading, LED lighting and an innovative air filtration system.
One of the main challenges in prefabrication in BIM construction is the necessity for working with tight tolerances from the start of the design process. This is aided by 3D modeling, as BIM construction brings the trades in early in process, driving a new design philosophy. Instead of onsite builders building to the design, designers now design to the module specifications, achieving substantial savings and compressing construction schedules.
Another stumbling block is what is known as multitrade prefabrication . Common in Europe, but almost unknown in the US, this involves the creation of modular units with duct work, gas mains, hot water supply, electrical conduits and communication pathways built-in. Independent prefab firms in Europe have developed BIM construction software for these horizontal systems that convert the model into a bill of materials on a module by module basis. The need for multi-trade coordination in the design of these modules is obviously necessary.
Another challenge is the task of lifting and manipulating these large modular units on the work site. With stick-built construction, only raw materials are handled by individuals or well-developed machinery systems. New systems and logistics will now need to be devised to transport, store and place the multi-ton, large-dimension assemblies that are a result of BIM construction prefabrication.
On the flip side, the advantages of modern prefabrication and modularization in BIM construction are overwhelming. So much so that the McGraw-Hill SmartMarket Report: Prefabrication and Modularization: Increasing Productivity in the Construction Industry reports that their survey shows that 98% of all architects, engineers and contractors expect to be using prefabrication and modularization to some extent in the projects. Healthcare facilities (49%), hotels and motels (11%), commercial warehouses (11%) lead the way in using BIM construction driven prefabrication. The building elements most conducive to prefabrication and modularization are building superstructure (27%), MEP systems (21%) and exterior walls (20%).
The reasons listed in this report for using prefab and modular systems include: improved project schedules, reduced costs and budgets, site safety improvements and green building/waste reduction.
The ability of modern prefabrication to provide a spectrum of customization possibilities is an important part of the new surge in acceptance of BIM construction modularization. The maturation of the manufacturing industry now provides sophisticated understanding and processes of the customization spectrum which can translate to the burgeoning sector of BIM construction prefabrication.
The terms made to stock (MTS), assembled to stock (ATS), made to order (MTO), and engineered to order (ETO) are used in manufacturing to define the extent to which a product is customized. This is generally considered proportional to the cost and lead time necessary for production.
This allows owners to achieve both a uniquity of design along with the savings of prefabrication. No longer does modular and prefab mean drab and boring. In the modern era one no longer needs to sacrifice aesthetics for the efficiencies of factory production.
BIM construction, in and of itself provides many benefits to the AEC industry. But its ability to lay the groundwork, along with IPD and new contractual landscapes, for modern prefabrication and modularization, heralds an almost revolutionary change in commercial building.
For more information about BIM construction visit O Donnell & Naccarato BIM:
Dennis Mordan (dmordan@o-n.com)
Jon Brazier (jbrazier@o-n.com)
877-854-9783
www.o-n.com
If you are looking for more information on
BIM construction
Please visit: www.o-n.com
Article Source:
ArticleRich.com